21世紀に入った今日、日本の自動車業界は真に世界をリードする立場にあります。新製品の開発技術、利用現場に於ける品質の高さ、また環境に対する先進技術の具現化は日本のいずれもメーカーも世界的に名声を得ています。しかし、それを築き上げた底辺には1950年代に於ける国の指導と共に、多くのメーカーは戦前&第二次世界大戦中に於ける技術の遅れを取り戻す為に、欧州メーカーに指導をいただいたものです。それは新製品を開発することではなく、主に既存の車種を生産&製造する技術習得でありました。
日野自動車も例外でなく、当時のフランスのルノー公団と手を結びました。今日の日本自動車産業の技術はその時代の先人達の想像に絶する努力、また世界に羽ばたくための大いなる志があったに違いありません。これらの精神はいまのビジネスでも忘れてはならないと考えます。
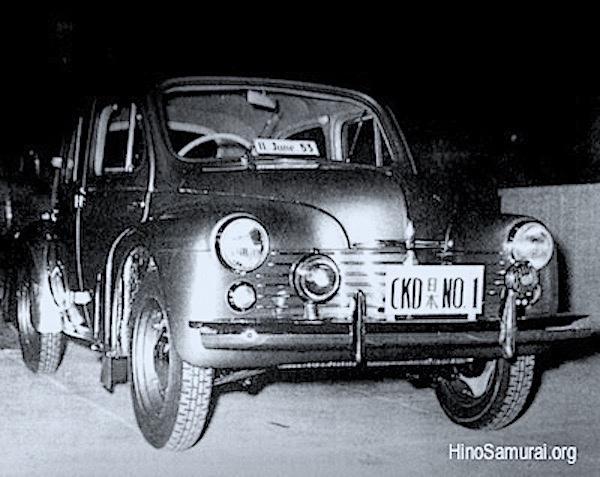
1953年6月11日 - 記念すべきルノー日野のノックダウン一号車
以下は当時の資料によるものです。(文責:江澤 智、2004/09/23)
フランス・ルノー公団からの届いた梱包(保税倉庫から引取)を解体。ルノー4CVのボデー構造が如何に合理的に出来ていたのが明解に分かる。同じ容積の箱のどう沢山の部品を詰め込むかだ。フランスの合理性の文化の賜物か?この様にしてルノー4CVは中国を含む世界で生産されたのだ。(補足:ルノー 4CV 国産化 CKD方式による組立状況 (1953〜1954) を参照)
以下は、カラー画像により当時の工場の雰囲気である (1955年10月 モーターマガジン “日野” 自動車産業をみる) :
【完成車置場】
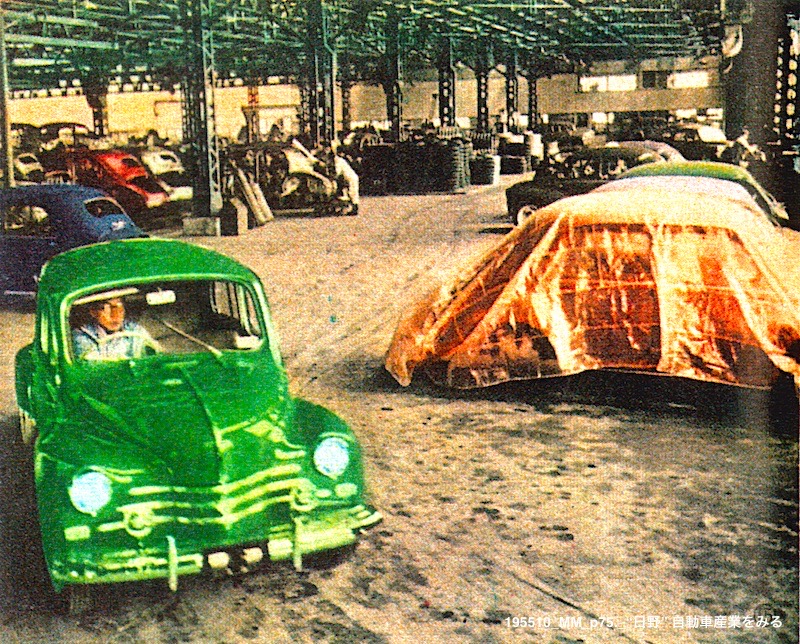
【赤外線乾燥室】
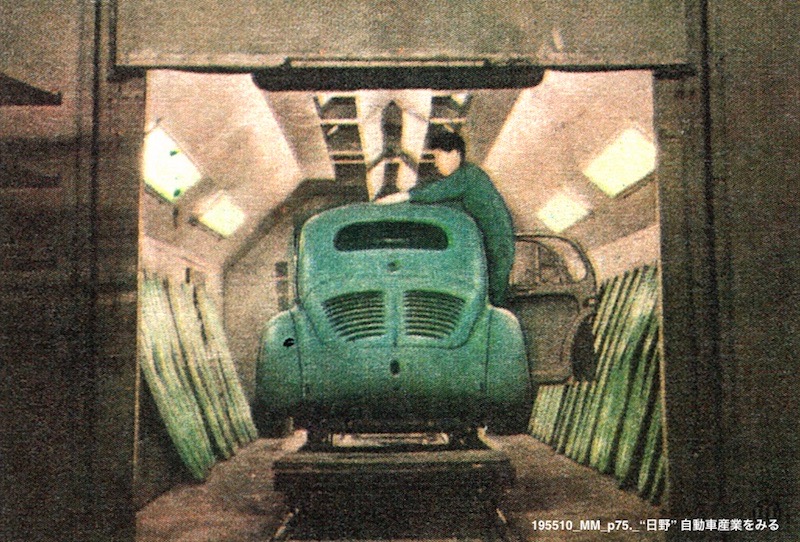
【組立台上のエンジンに上方からボデーがつり下げられて取り付けられる】
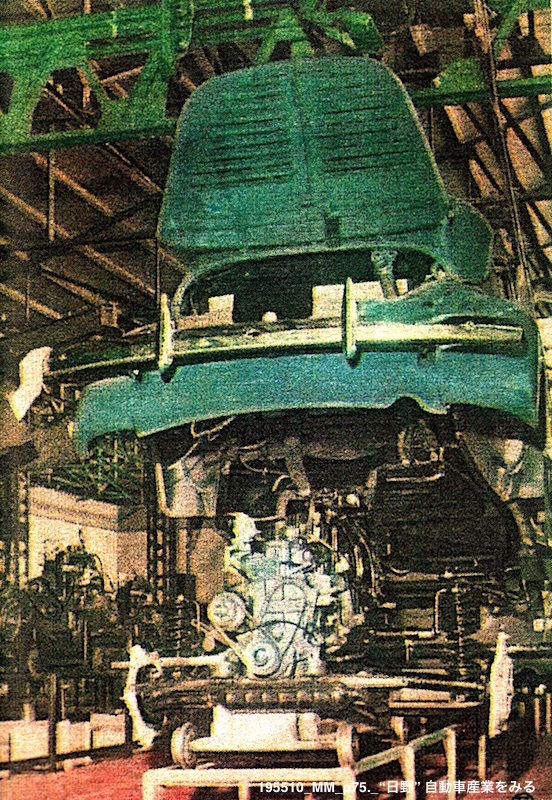
【組立ライン上完成間近なルノー】
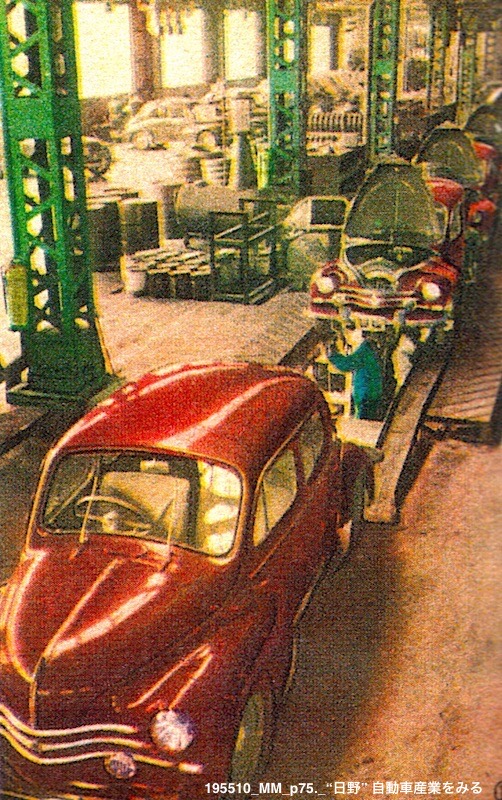
ルノー4CV国産化による自動車製造技術の飛躍的発展(日野自動車資料より)
1. 生産技術部の設立
フランスのルノー公団との「ルノー4CV」国産化契杓に当り、l953年(昭和28年12月、日野自動車に「生産技術部」が設立された。これはルノーとの提携時に受領したドキュメント、訪欧調査の結果、設計と製造のあいだのシステマティックな機能を果たす部門の必要性を認識したためであった。大量生産においては設備、道具、工法の標準化が達成されていないと、高品質で、しかも均質の機能をもつ製品を生むことはできない。ルノーとの提携と生産技術部の設立は、日野自動車にとって、初めて生産活動に本格的なシステム思考を導入、実践する端緒を開いたことになる。
2. 自動車を創る技術の体得とシステム技術の視点
ルノー4CVの国産化に当り、ルノー公団より車の設計から生産までの膨大な資料と図面が送られてきた。これらの資料の翻訳は言葉の翻訳だけでなく、技術を翻訳・理解する作業であった。また、日野自動車にとって、まさに発想転換の維新ともいえる経験であった。生産技術面でいえばIE的モノの考え方に基本をおいた、プラント計画、レイアウト、工程計画、設備計画の実施である。また製造、鍛造、プレス、板金、溶接、機械加工、熱処理、表面処理、塗装、組立、倉庫など生産工程の技術検討が不可欠な要素であった。さらにこれらをコントロール、管理する工程表、技術標準、時間設定に至るシステム作りも重要課題だ。こうして近代自動車工場の実際を非常な短時間に体験したわけだが、この経験があとに続くコンテッサの間発、中型トラックの技術開発に多大な貢献を果たしたのである。
3. 国産化のステップ
ルノー4CVの国産化は一気になしとげられたわけではない。段階を踏んで、はじめて100%の国産化が達成された。
- 第1ステップ…完成車組立(板金組立一塗装一総組立)
日野工場東北部(現機構RE実験工場の建物)に1200坪のCKD工場(ホワイトボディAssy - paint - 艤装 - 検査タッチアップラインを含む)建設、月産200台をねらい設備設定をした。昭和28年3月第1号車がラインオフし、国産化の第一歩を印した. - 第2ステップ…フロントアクスル、ステアリングシステム、クーリングシステムその他関連のユニット
- 第3ステップ…クラッチ、トランスミッション、デフ、リヤアクスル(各単品素材、部品、Assy)
- 第4ステップ…エンジン(素材、部品、Assy)
- 第5ステップ…ボディ(プレス品、ユニットAssy、ボディAssy)
4. ルノー国産化部品の製作は生産加工技術の常識を変えた
すべての基本は工程表(GUMガム)、工程図(フィッシュ)、時間研究(MDT Rating)から始まる。これらの実施は生産技術者が設計部門と製造部門との間に立って果たすべき役割の一つで、レイアウト、設備準備の前提条件である。
この一連の作業は、30年代中期のIE時代、小型車新工場建設ブームの先がけとなった。ルノーのBNA規格、材料、熱処理、工具、各種材科試験規格、設備、治具、運搬具の諸資料の入手、展開は生産準備に対するきめの細かさの必要性を十分認識させ意識改革となったといえる。主な特長をあげる。
- 工程の分割、集合と流れを考えたレイアウトの実施
ルノー部品の加工、部分組立、プレス~ホワイトポディ、塗装、総祖立について、オーソドックスな時間見積りと工程分割、編成を行ない、レイアウトに反映した。現在の工程表、技術標準はこの時に基礎を築いたといえる。 - ホモロゲーションによりIE、QCを踏まえた生産加工技術を習得
ホモロゲーションとはフランス語のHomologationで認可、公認を意味する。ルノーの国産化に際してすべての日本製国産化部品をフランス本国に送付、その認可を必要とした。しかも国産化契約5年以内に実施するわけである。そのためには資料を読みこなし、モノに触って見るだけでは規格に適合する製品はつくりえない。
そこで、板金から、機械加工、鋳造、鍛造、塗装、組立まで関係各部門の中堅技術者・作業員が大勢渡仏し、あらゆる技術の吸収に努めた。一方で生産技術部門の拡充と生産加工技術の会得、設備の入手、ラインの設定に全力を注いだ。- 高周波焼入れ、ガス浸炭技術の導入は材料選択、強度に対する考え方の常識を変えた。
軸物(クランクシャフト、アクスルシャフト、…)など高強度部品にはニッケル、クローム鋼などが使用されていたが、焼入れ条件菅理、焼入れ深さ制御(均一焼入深さ、硬度等…)の面で中炭粗鋼への転換が可能になった。品質の安定は形状のサイズダウン、高強度、高靭性を実現した。
さらに大型トラックバス部品へ展開効果もすこぷる大きかった。熱処理工場内で実施していたこの焼入れは、やがて機械加工工程ラインの中に組み込まれ、イン・ライン化を実現。これは業界でも当社が草分であった。 - ギヤ加工精度の向上は車の騒音をイッキに低くした。
ギヤのかみ合い騒音はRR(リヤエンジン、リヤドライプ)車の宿命である。しかし、ルノーは静かな車であった。それは数多くのギヤがスムーズにかみ合い、音が低く抑えられているからだ。ホモロゲーションで一番苦労したのがこのギヤの加工技術であった。生産性が高く、加工精度も高いギヤを製造するためにグリーソン社製歯切マシン、ガス浸炭設備、クェンチングプレス、研磨盤、防音室の重荷重、高速回転の設備を生産ラインに採用した。特に、熱処理工場として中間熱処理工場が新設(32年)された。
また、いち早くギヤの研摩を採用するほか、かみ合い率を変え、かみ合い騒音に対処し、大きな効果をあげた。これはその後の大、中型車にも適用、騒音低減と強度向上に寄与している。 - ルノー部品の鋳造はフィードフォワード的考え方を導入した。
薄肉、軽量、高品質(寸法精度・少ない鋳造欠陥、鋳肌)の鋳物造りは、これまでの鋳物職人への依存から脱却しなければならなかった。すなわち、冶金学的検討と鋳造法案(工程、技術標準)の設定、型の設計製作、鋳物条件管理の容易な設備設定などの導入と実施である。
こうして実施されたシリンダブロック、アルミヘッド、トランスミッションケース等の国産化は量産鋳造技術、管理技術を習得するなど当社の鋳物技術に大変革をもたらした。特にへッド、T/Mケースのアルミ鋳造金型の設計から製作、グラピティ鋳造技術、へリサート用異種金属の鋳込みなどかなりのノウハウを得た。 - 薄板の成形技術は多くの波及効果を生んだ。
戦車の製造から始まって大型トラック、バス、特車を作っていろメーカーにとって薄板とはせいぜい1mm位の厚さが常識であった。それがいきなり0.6mm厚さの美麗な冷間圧延板である。しかしこの薄板が軽量モノコック構造に不可決のものであった。
パーツのプレス、ユニットAssy、ホワイトボディAssyと最も国産化の中で、勢力を注いだのがこの薄板の成形部門である。また小型乗用車の場合サスペンション廻りもまた、薄板プレス成形品の組合わせ構造である。ここでも従来のハシゴ形状フレームと異なった生産技術が要求された。すなわちバックスプリングのない精度の高い、しかも表面品質(なめらかさ、無しわ、適切な伸び等)の良いプレス成形品の製造であり、熱歪や溶接跡の少ない溶接、接合、打出し板金とアーク溶接の軽験しかない者にとってはこのようなプレス成形や接合は正に新技術の洗礼を受けるに等しかった。
モノコックボディの国産化、これは誰もが経験していない分野の作業であった。従来の設計部門と生産技術部門の混成協業でフランスの図面の翻訳、原寸図作成、日野規格の適用、型図面作成、型製作と一連の国産化作業を遂行している。一方0.6mm冷間圧延鋼板は当時の鉄鋼メーカーでは不可能で0.7mmに妥協している。一方接合技術面ではアーク溶接に変わり、抵抗溶接(特にスポット溶接、シーム溶接)が導入された。
シャシ部品に対してはフラッシュバット溶接(アクスルパイプとフランジの接合)が採用されている。
当社のスポット溶接、シーム溶接、プロジェクション、フラッシェバット溶接の歴史はこの時に始まったといって良い。また、成型関係の設備では1957年(昭和32年)には本格的な1400トンやトリプルアクションプレスを中心としたプレス工場が誕生している。
以後、コンテッサ900、1300、中型トラックキヤブ、ハイラックスとその技術は引きつがれていくのである。
- 高周波焼入れ、ガス浸炭技術の導入は材料選択、強度に対する考え方の常識を変えた。
近代的自動車工場への幕開け(日野自動車資料より)
昭和30年代の後半の高度成長期は、同時にマイカー時代の先がけの時期でもあった。その時代のニーズに応えて、自動車メーカー各社は、新工場の建設を競っていた。日野自動車では、コンテッサの専用工場が建設された。また、生産の諸設備の新設、充実も目覚ましいものがあった。主なものは、
- グリーソン社製歯切機械の大量設備
- トランスファマシンによるシリンダブロックの流れ加工
- サンドスリンガー式の鋳造設備
- 2000tプレスを中心としたプレスライン群ジグウェルダー
- スポット溶接の大量設備
- P&Fコンベア、フロア、台車コンベア、ハンガーコンベアを縦横に利用した塗装組立工場
- 組立から検査まで一貫したラインを組んだエンジン工場、
などがあげられる。近代化的流れ方式と自動化が遺憾なく発揮されろ多量生産の時代が来たのであった。
それと同時に進められたのが協力メーカー、外注メーカーのピラミッド型の系列化の促進であった。つまり、量産規模が月産500~1000台を超えると、原材科の鋼板、鋳鍛材料を除いて、自社内での生産能力に限界が見えてくる。そこで、素材づくりから、加工、Assyまでの各工程での外注依存が進み、その結果が系列化であり、また部品専門会社の成長であった。
補足:ルノー 4CV 国産化_ Localization of Renault 4CV by Hino Motors (1952-1954)
01_CKD梱包部品_ここで開梱作業は行われ脱脂工程に運ばれる。
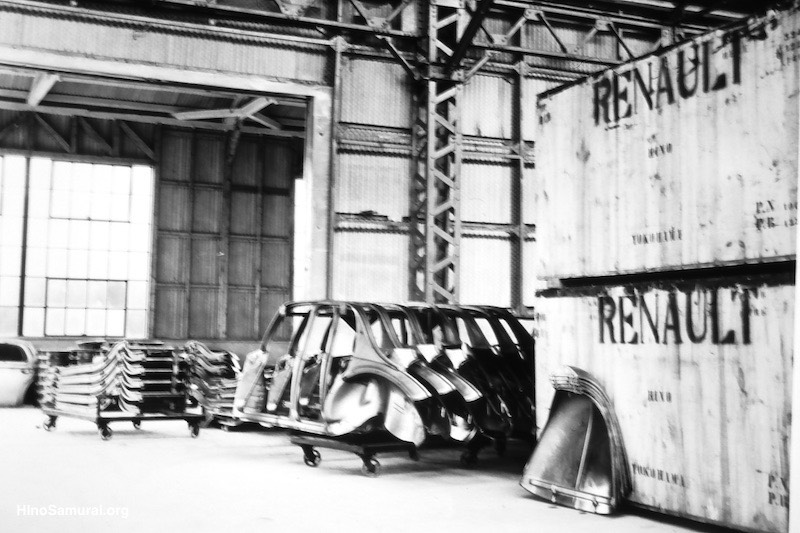
02_塗装ショップ_防錆油の脱脂(アルカリ脱脂)、梱包部品防錆は驚くほど徹底、専用タンクで実施。薬品は日本ペイントと共に開発。
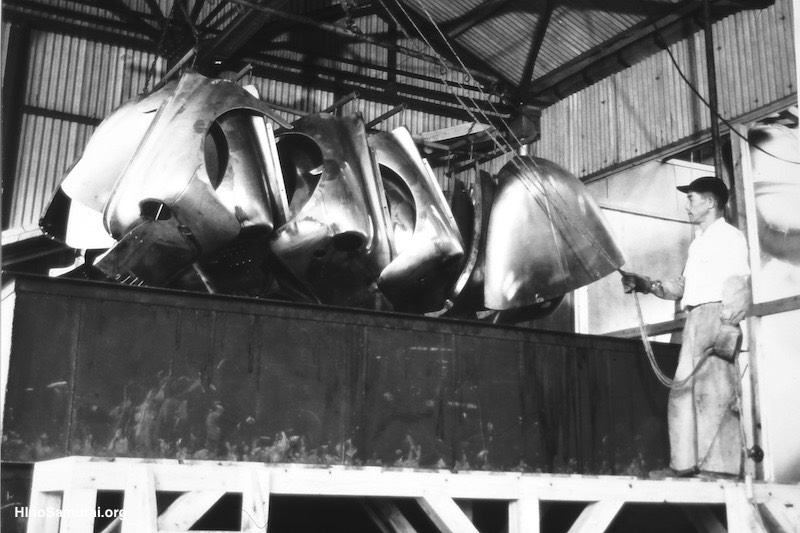
03_塗装ショップ_防錆油の脱脂(アルカリ脱脂液タンク内)。
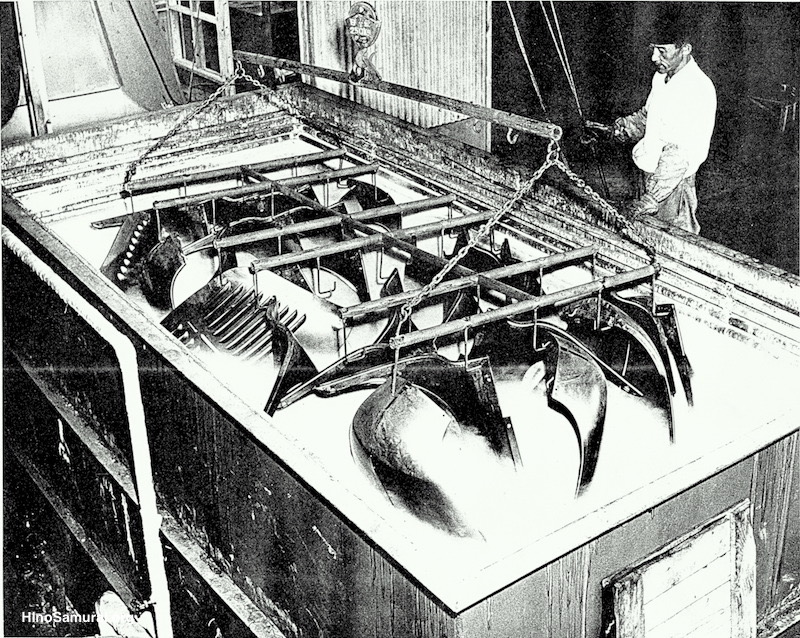
04_ホワイトボディ組立ショップ_スポット溶接が導入され,我が国初のコノコックボディは組立てられた。
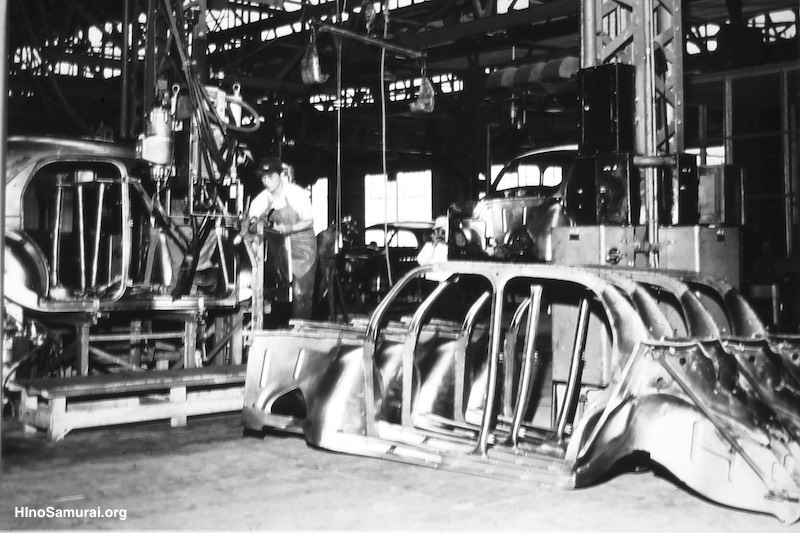
05_ホワイトボディ組立ショップ_フロント・フェンダー部、スポット溶接。溶接機はかなり大きい。
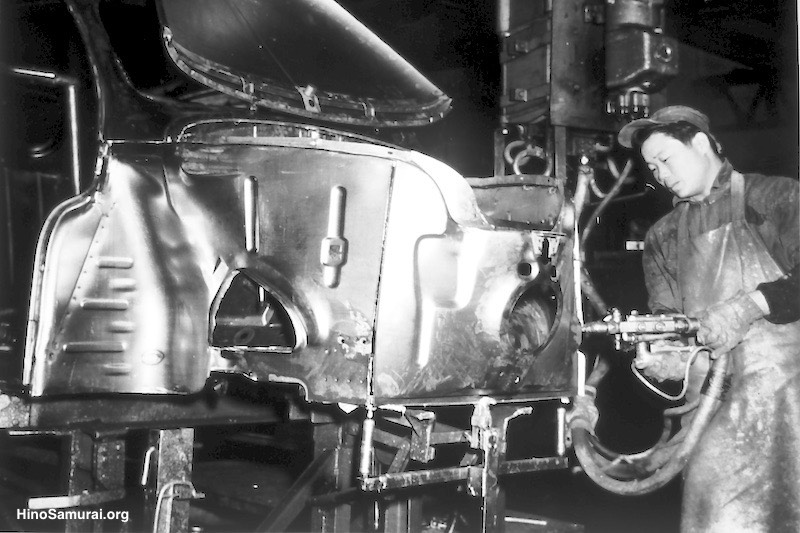
06_ホワイトボディ組立ショップ_ ドア開口部、グラインダーによる修正作業。
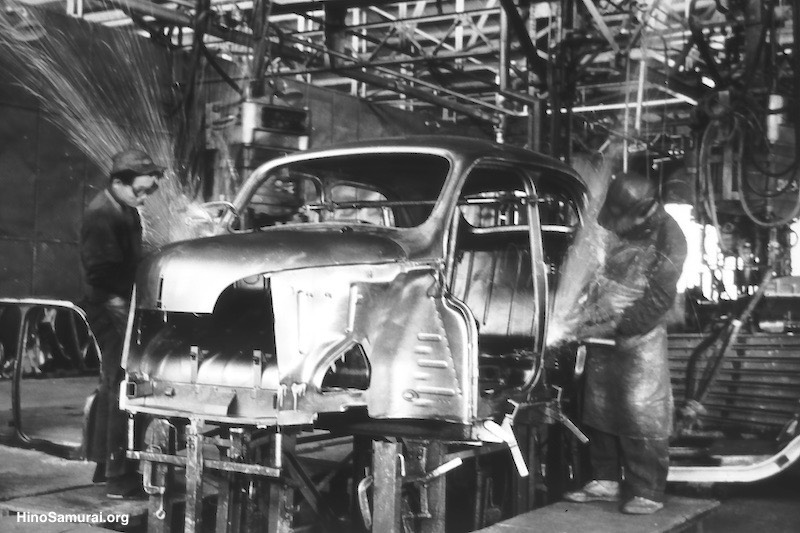
07_ホワイトボディ組立ショップ_定置式ステーションで作業が行われる。ここでは部分的にガス溶接作業をしている。
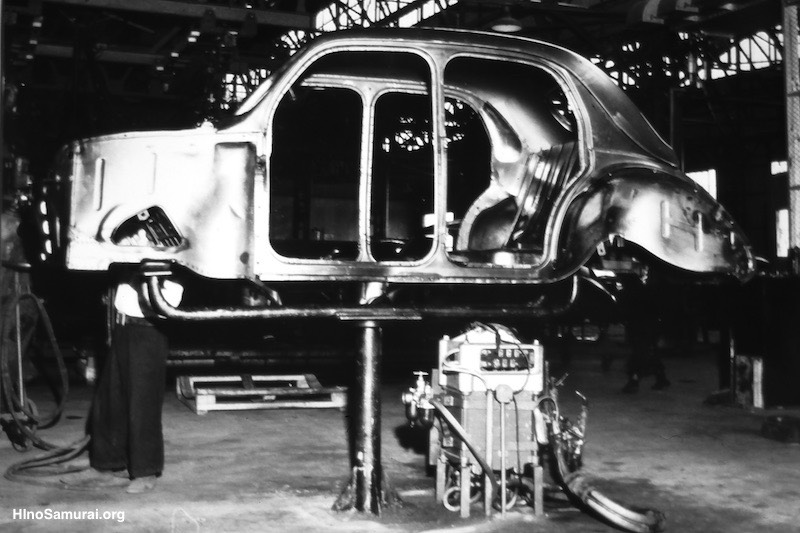
08_塗装ショップ_アンダーシール(アンダーコート)は日本特殊塗料製。ホイストで吊上げ塗布。当時の車と比べ格段に皮膜は厚い。
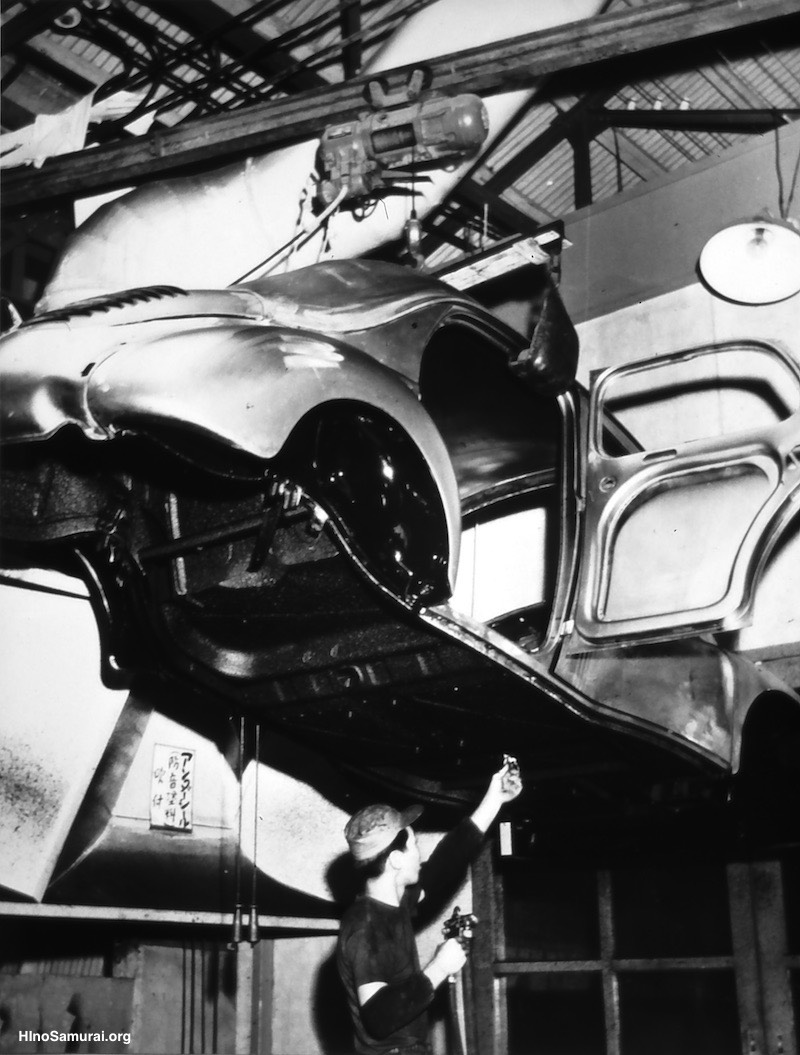
09_塗装ショップ_乾式塗装ブースでの上塗り塗装。焼付型エナメル塗料の使用は我が国ではじめて。
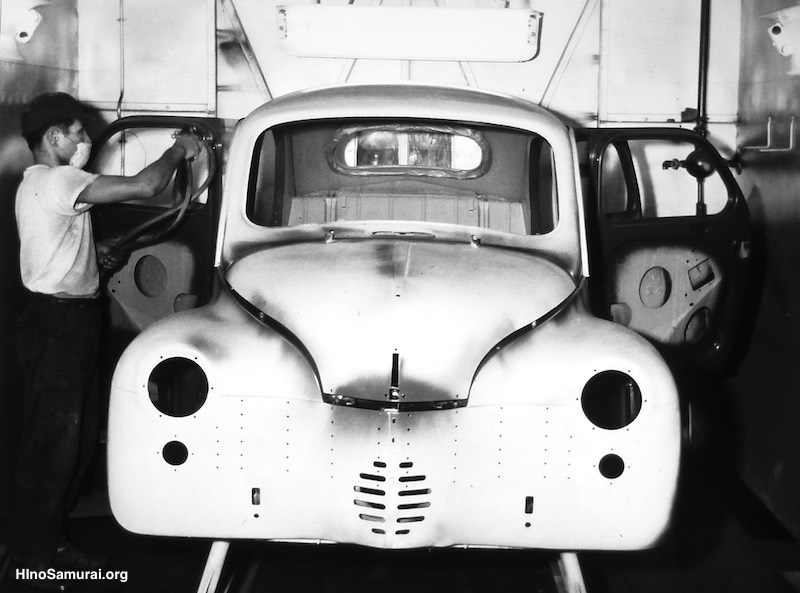
10_塗装ショップ_熱風乾燥炉。120〜130度(摂氏)。30分の焼付塗装。さすがに光沢はすぐれていた。
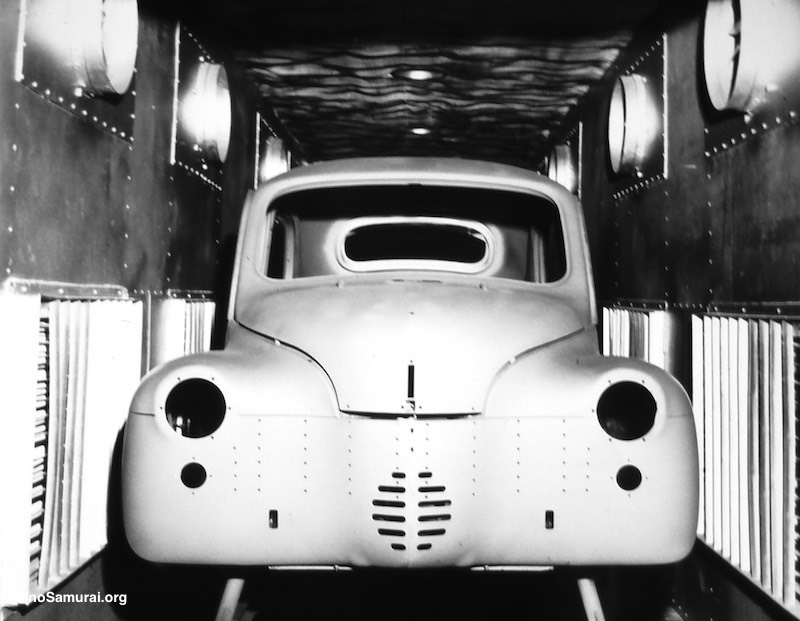
11_塗装ショップ_上塗塗装工程、乾式ブース、天井にフィルターあり。
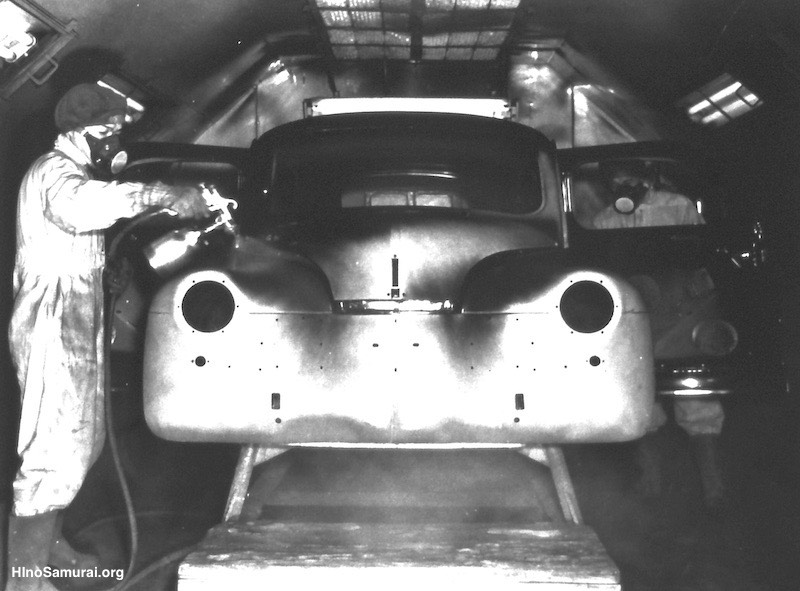
12_塗装ショップ_水研ぎ工程。頭巾、ゴム製前かけ、ゴム長靴、青い作業衣が女性の服装である。当時は低賃金の女性労働者は普通だった。
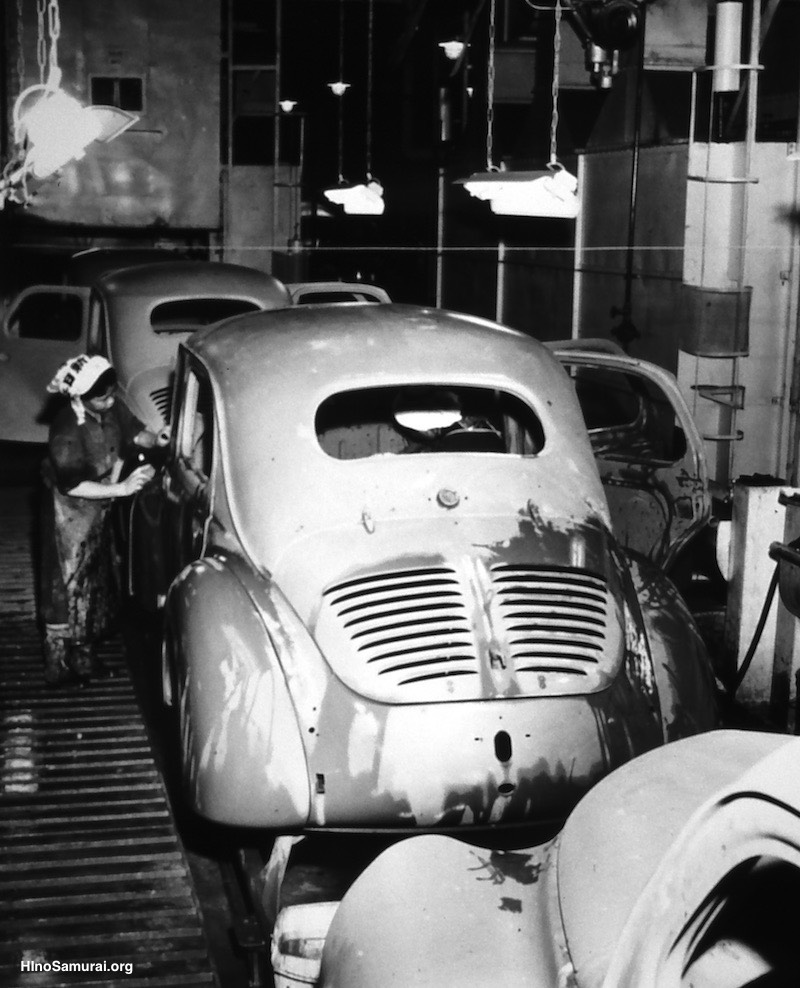
13_塗装ショップ_水研ぎ工程。老若女性が大勢いる。男は部品塗装。右は上塗り塗装工程。
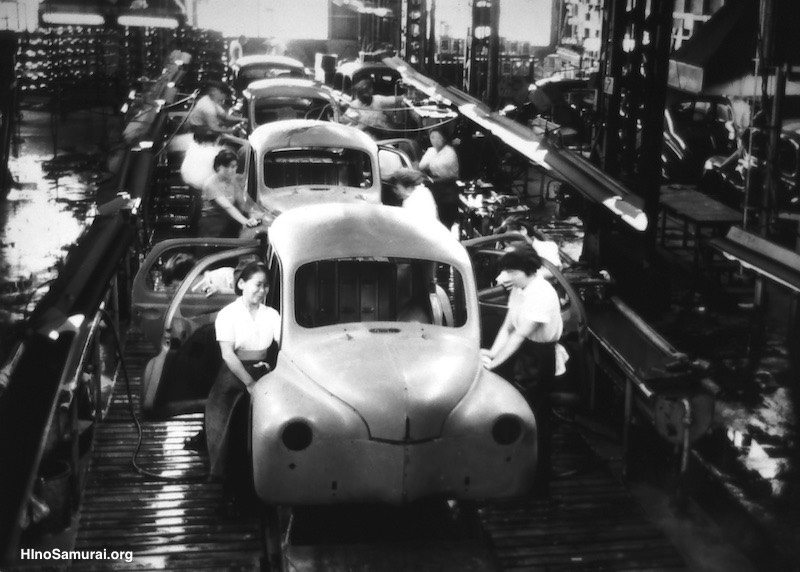
14_艤装ショップ_台車上で内外装部品組付け実施(手押し台車)。
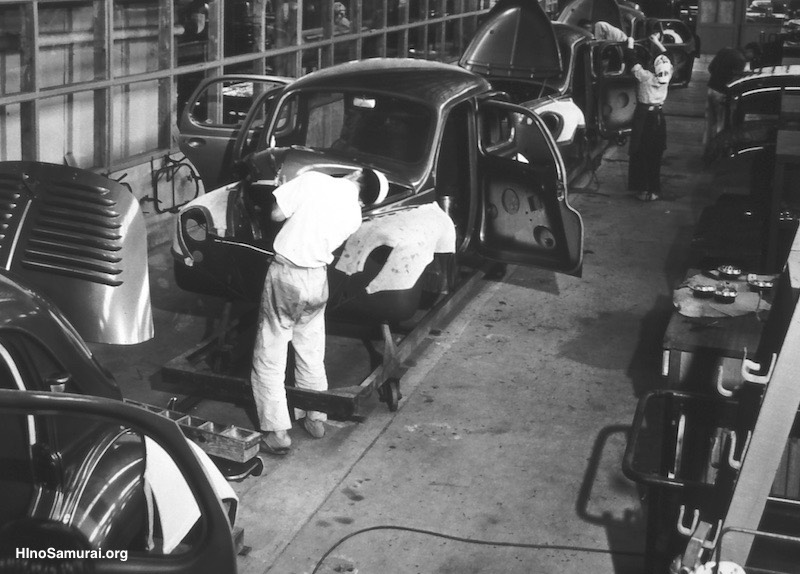
15_台上組立ショップ
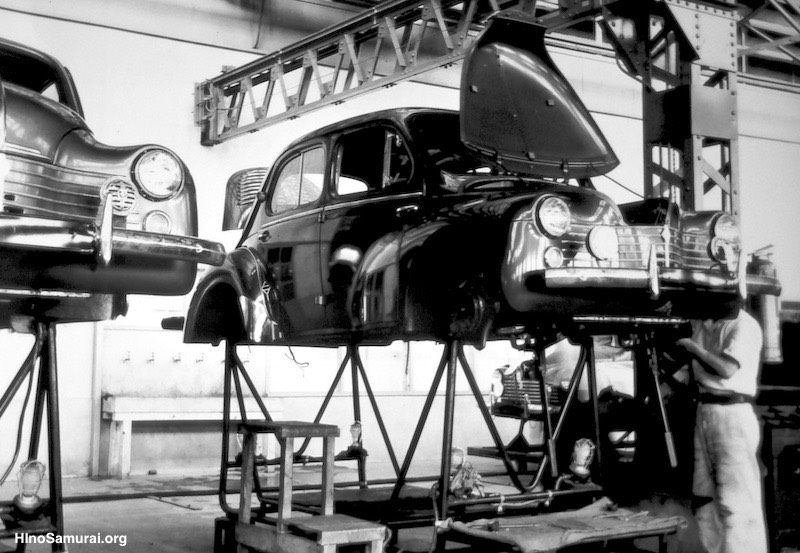
16_台上組立ショップ(55年型)
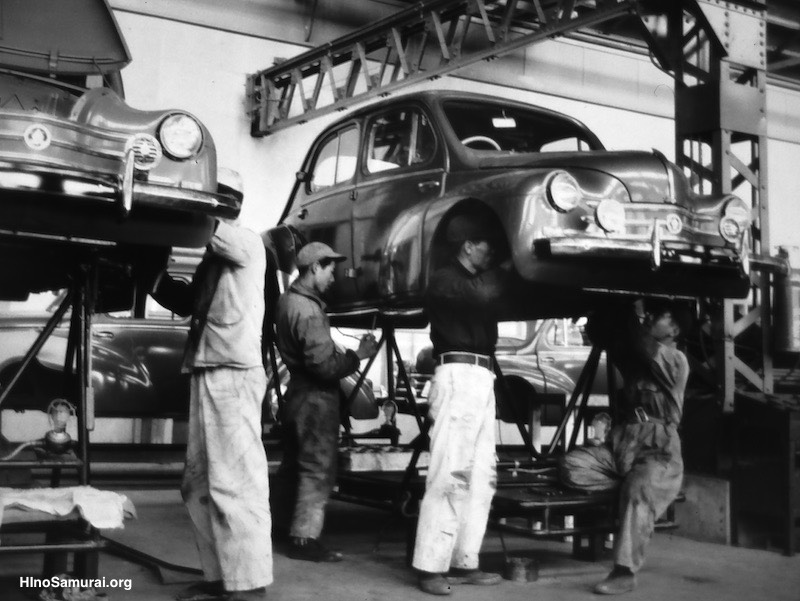
17_総組立ライン_ボディ、パワーユニット結合。
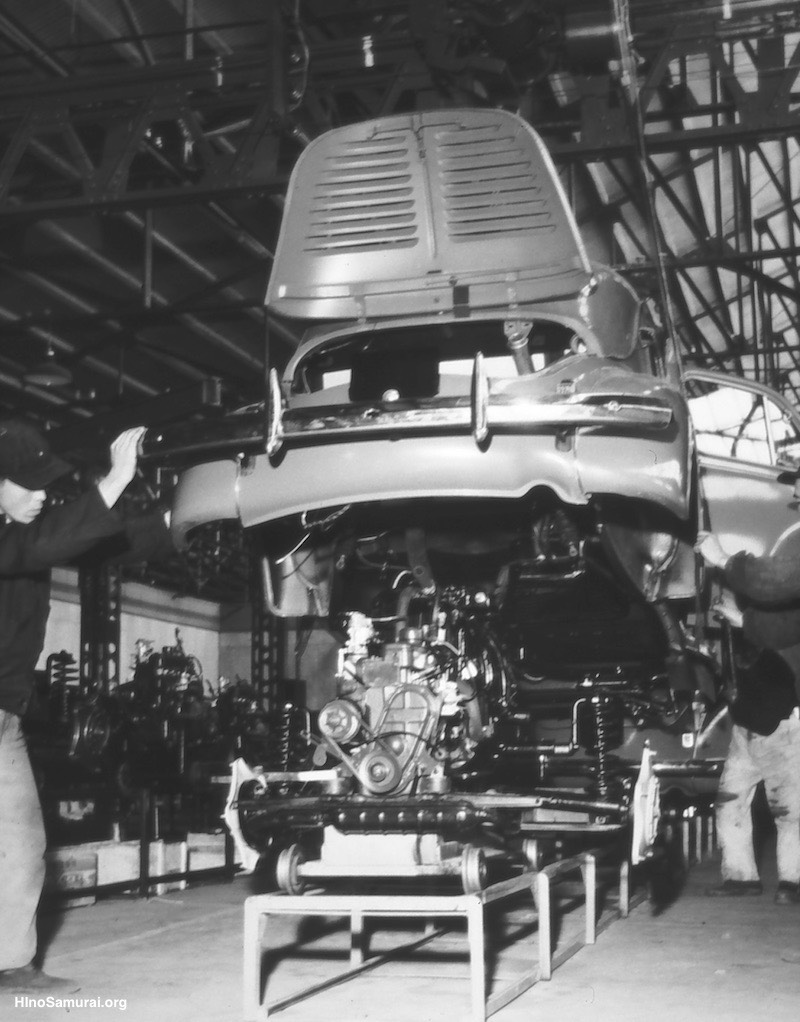
18_総組立ライン_最終組立工程(ピット)

19_総組立ライン_最終組立工程(55年型)
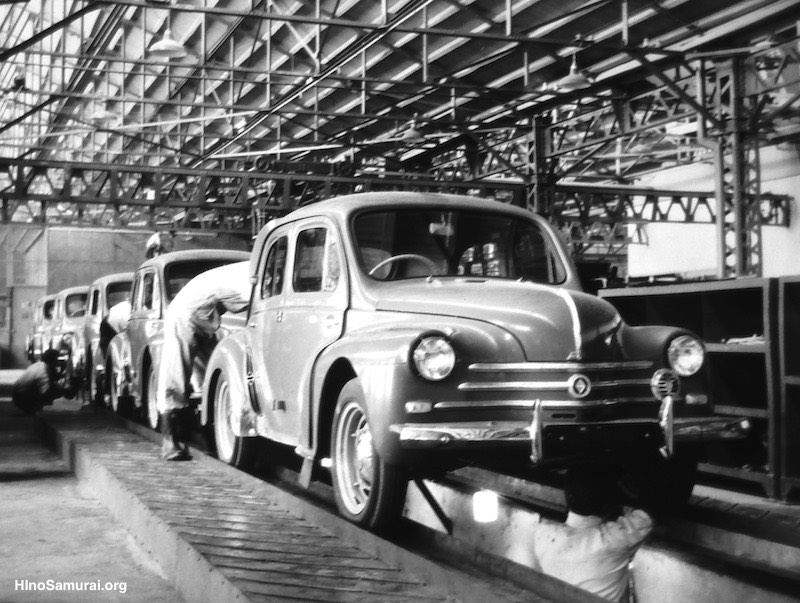
20_総組立ライン(ピット作業),遠方はタッチアップ工程。
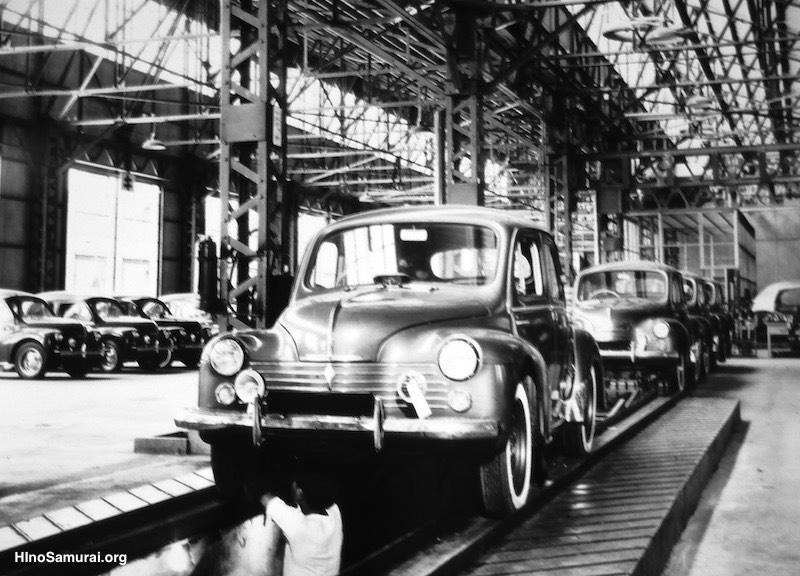
21_タッチアップ・ショップ(55年型)
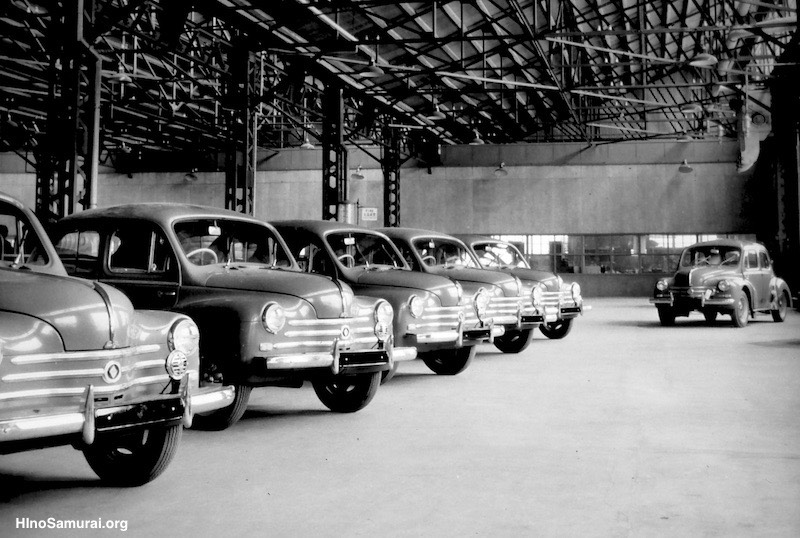
22_完成車ストレージ(54年型)
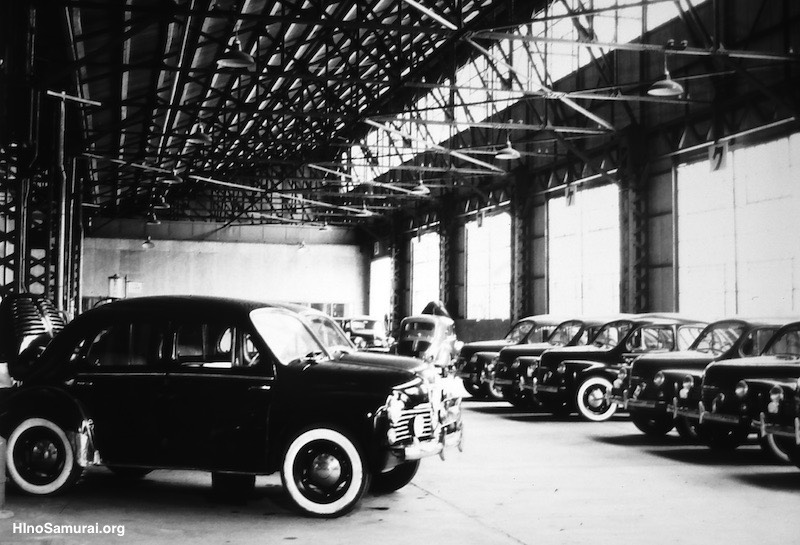
23_完成車ストレージ(54年型)
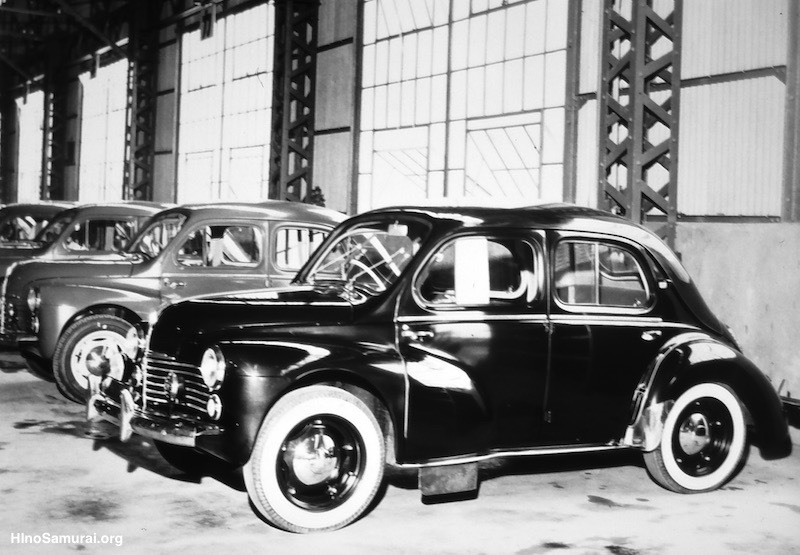
24_ルノー4CV(PA デラックス)55年型。フロントグリルが太い3本線に変わった。
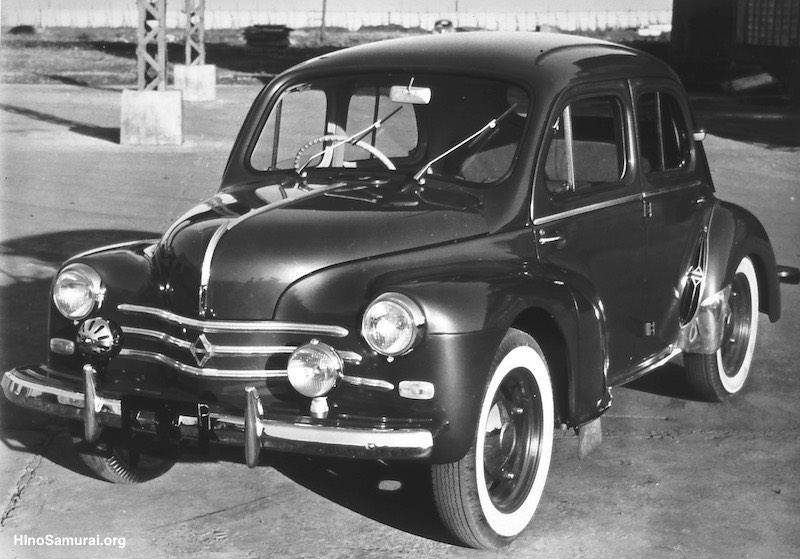
本ページへのコメント&意見はこちら迄 (実名表記にて) 。
Any Comments to here would be appreciated (Please Use your one name)